The Water and Wastewater industries are expansive, with hundreds of areas which can experience damage. This blog will be focusing on three in particular –pumps, pipework and tanks. As these are some of the most common places within the industry where polymeric materials can be used to repair, protect and improve assets.
Pumps
Firstly, we´ll be looking at pumps within the industry. These can suffer from many damage mechanisms, with the primary being:
- Deterioration due to corrosion
- Deterioration due to erosion
- Impact, chemical attack etc.
Erosion and Wear
Pumps and pipework are under the constant threat of erosion and wear as they handle large quantities of liquid throughout their working day. Entrained solids can damage pump elements and casings can be eroded by constant water flow and corroded by chemicals, sewage and other materials involved in the treatment process.
Long lead times from manufacturers often means that an out of service pump can cause lengthy delays and shutdowns and outright replacement is often prohibitively expensive.
When on site, we need to look for evidence which suggests the cause of damage, so that we can identify the root of the problem. Starting with the above photo, we can see damage from entrainment, or solids suspended within the flow.
If this is compounded with corrosion caused by aggressive substances within the flow or sewage, then we can see erosion-corrosion. This is where corroded steel is eroded away, thereby exposing fresh steel which then corrodes and the process repeats, resulting in severe metal loss.
Most asset owners would probably discard this pump and replace it with a new. However, it is possible to restore these pumps to bring the efficiency back up for the long term using epoxy solutions.
To repair, the first step would be to grit blast the pump. Effectively serving two purposes:
- Firstly it removes all the loose, friable rust and metal, cleaning the surface. Secondly it provides a profile or key for the epoxy to adhere to.
- Next you use a paste-grade epoxy to rebuild the profile of the pump internals and components.
- Finally you apply a protective cermaic coating to provide long-term protection against erosion and corrosion.
Based on previous experience the cost of an epoxy solution is approximately 20% the cost of replacing the pump outright.
Cavitation
Another form of damage we may see is cavitation, the evidence of which you can see above. The typical sign of cavitation is localised micropitting, caused by the collapsing of steam bubbles near the surface. This most often occurs in areas of low water pressure, particularly trailing edges of impellers where the pressure is low enough to allow water to boil.
Given the impact nature of cavitation, this calls for a solution with high toughness, as a hard ceramic solution would be too brittle and lack the toughness to withstand the energy of impacts. Therefore, an elastomeric system is used to protect equipment against cavitation. This polyurethane can withstand the deformation caused by cavitation microjetting.
Learn more about products for pumps here.
Pipework
We’re now moving on to pipework solutions. Pipes suffer from damage both on the external and internal diameters from both erosion and corrosion.
- Externally we may see environmental attack, which calls for a solution where a barrier is formed between the pipe and the environment.
- Internally we may see damage from erosion and chemical attack, possibly at high temperatures.
These forms of attack both lead to loss of wall thickness, which may eventually lead to live leak situations, often causing the asset to be taken offline whilst it is repaired or replaced . This downtime can be very costly, but by using an epoxy solution these costs can be avoided.
Restoring pipework
To restore the integrity of pipes, reinforce equipment, and seal leaks, a polymer solution can be used, either through local sealing or a fully encapsulating Superwrap.
To protect against future damage, an internal coating can also be applied inside the pipe to guard against erosion and corrosion. This can be done either manually or with a spin-spray method.
Coatings can provide protection against erosion, corrosion, and chemical attacks, even at high temperatures.
External and Internal Wear on Tanks
The roof of the tank is subject to rapid degradation due to corrosive vapors from the medium stored in the tank. The walls of tanks can also be susceptible to corrosion, with welds being particularly vulnerable points for leaks.
Microbiologically influenced corrosion (MICR) can occur on the substrate. Chlorides and sulfates present in the medium can corrode the inside of steel containers. The inside of concrete tanks can erode when submerged in water or corrode due to chemical attacks, leading to cracks and leaks, which in turn compromise the efficiency of the facility.
By using coatings, the inside of tanks and containers can be protected, typically with a chemical-resistant coating. This is a durable and effective solution, making it an excellent alternative to time-consuming repairs or replacements. Another advantage is that carbon steel tanks can be used instead of stainless steel tanks, which helps to keep costs down.
A solution to problems with tank bottoms is a tank base protection system, which works by applying a product together with a reinforcing fabric. The seal is a flexible membrane, allowing a breathable effect. Liquid cannot penetrate the membrane, but moisture can escape. This creates a dry underside.
Concrete damage
The wastewater treatment process and related activities expose concrete to a variety of damage mechanisms including:
- Erosion-corrosion
- Physical damage
- Chemical and microbiological attack
- Carbonation
- Freeze-thaw cycles
High relative humidity levels, the need for cold temperature curing and the requirement to keep operations running smoothly make repairs increasingly difficult.
By using a concrete repair composite designed to rebuild and repair damaged concrete surfaces, you can restore the original profile with a simple procedure that minimises downtime and can be completed without hot work. Belzona concrete repair systems will cure in a matter of hours, achieving full mechanical hardness soon after. Specialist coating solutions can then be applied to improve resistance to the common forms of wear and corrosion, extending service life with a minimum of financial outlay.
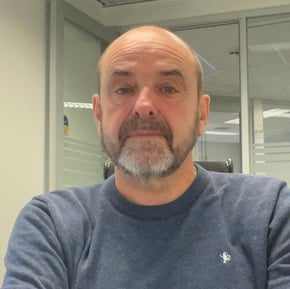